高精度部品はどのように加工されるのか
2023-09-22
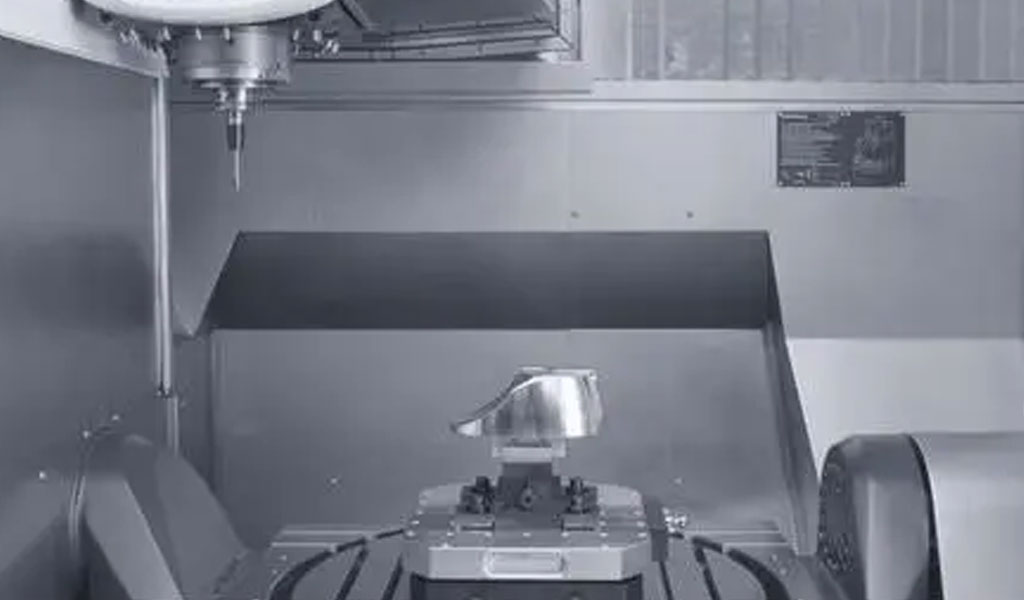
精密加工を理解する
精密機械加工は現代の製造業の基礎であり、幅広い業界で使用される複雑で正確なコンポーネントの製造を担っています。 その重要性を十分に理解するために、精密機械加工の核となる概念、さまざまな分野における精密機械加工の重要な役割、そして現在の卓越した状態に至るまでの歴史的な歩みを探ってみましょう。A. 精密加工とは何ですか?
精密機械加工とは、高度な精度と制御でワークピースから材料を除去する一連の製造プロセスを指し、その結果、厳しい公差で精巧に作られたコンポーネントが得られます。 このプロセスでは、金属、プラスチック、セラミックなどの原材料が、厳密な仕様を満たす精密な部品に変換されます。 精密機械加工の主な特徴は次のとおりです。- 正確さ: 精密機械加工により、最終製品が意図した設計に正確に適合し、誤差が最小限に抑えられます。
- 厳しい公差: 非常に厳しい公差で部品を製造できるため、完成した部品が指定された寸法に厳密に準拠していることになります。
- 優れた表面仕上げ: 精密機械加工により優れた表面仕上げが得られ、多くの場合、追加の仕上げプロセスが不要になります。
- 複雑な形状: 複雑な形状、輪郭、機能を作成できるため、複雑なデザインのコンポーネントの製造には不可欠です。
- 再現性: 精度 機械加工プロセス再現性が高く、複数の部品にわたって一貫した品質を保証します。
- 多才:幅広い材質に適用できるので、様々な産業に適しています。
B. 精密加工の重要性
精密機械加工はいくつかの重要な産業において非常に重要な意味を持ち、私たちの日常生活のさまざまな側面に影響を与えます。 その重要性について、説得力のある理由をいくつか挙げます。- 航空宇宙産業: 航空宇宙分野では、極限の条件に耐えるコンポーネントを製造するために精密機械加工が不可欠です。 航空機エンジン、着陸 ギア、構造要素は安全性とパフォーマンスのために精密機械加工された部品に依存しています。
- 医療機器: 手術器具、補綴物、埋め込み型デバイスなどの医療機器には、生体適合性、精度、患者の安全性を確保するための精密機械加工が必要です。
- 自動車セクター: 精密機械加工部品は、自動車の信頼性と効率を確保するために自動車産業にとって不可欠です。 エンジン部品、トランスミッションシステム、ブレーキ機構などの部品には精密な機械加工が必要です。
- エレクトロニクスと半導体: 精密機械加工は、機能のために極小の公差が不可欠なマイクロ電子部品や半導体デバイスの製造において極めて重要です。
- エネルギー分野:エネルギー産業は、タービン、発電機、トランスミッションコンポーネントなど、発電に使用される重要な部品の製造を精密機械加工に依存しています。
- 工具と金型製作: 精密機械加工は工具や金型の製造において極めて重要であり、それらは他の無数の製品の製造に使用されます。
- 家電: スマートフォン、ラップトップ、その他の家庭用電化製品の製造では、洗練されたデザインと最適な機能を確保するための精密機械加工の恩恵を受けています。
- 研究開発: 研究者や科学者は、実験、プロトタイプ、実験装置用の精密機械加工コンポーネントに依存しています。
C. 歴史的展望
精密機械加工の歴史は、熟練した職人が初歩的な工具を使用して材料を成形していた古代文明にまで遡ります。 ただし、当時に達成された精度は、現代の標準に比べて限られていました。- 初期の精密加工: 18 世紀から 19 世紀の産業革命は、精密機械加工の発展において極めて重要な時期を迎えました。 旋盤やフライス盤などの工作機械の発明により、精度と一貫性が向上し、製造業に革命が起こりました。
- World War ll: 精密機械加工は、必要な精度と均一性を備えた軍用装備を製造するために不可欠であったため、第二次世界大戦において極めて重要な役割を果たしました。 この時代には、機械加工技術の進歩と新素材の出現が見られました。
- 戦後の進歩: 戦後、コンピューター数値制御 (CNC) 機械の使用を含む技術革新が急速に進みました。 CNC加工 自動化された高精度な作業が可能になり、製造業の新時代が到来します。
- デジタル時代: コンピュータとソフトウェアの加工プロセスへの統合により、加工精度がさらに向上しました。 最新の CNC マシンは、複雑な操作を比類のない精度で実行できるため、今日の製造現場では不可欠となっています。
素材とその意義
材料は精密機械加工の基礎であり、適切な材料の選択は高精度部品の製造において極めて重要な役割を果たします。 このセクションでは、適切な材料を選択することの重要性を掘り下げ、材料特性の重要性を理解し、機械加工性に影響を与えるさまざまな要因を検討します。A. 材料の選択
精密機械加工における材料の選択は、最終製品の性能、耐久性、機能に直接影響を与える重要な決定です。 メーカーは材料を選択する際に、いくつかの要素を考慮する必要があります。- 材料の適合性: 材料は意図された用途に適している必要があります。 業界や用途が異なれば、耐熱性、耐食性、導電性などの要件も異なります。
- 機械的性質: 引張強さ、硬度、延性などの機械的特性が重要です。 たとえば、航空宇宙分野では、構造コンポーネントには引張強度の高い材料が好まれます。
- 熱特性: 用途によっては、優れた熱伝導性や高温耐性を備えた材料が必要です。 これは、発電やエレクトロニクスなどの業界では特に重要です。
- 耐食性: 腐食が懸念される環境では、ステンレス鋼やチタンなどの耐食性の高い材料が推奨されます。
- 重量に関する考慮事項: 自動車や航空宇宙などの業界では、燃料消費量を削減し、パフォーマンスを向上させるために、アルミニウムや炭素繊維複合材などの軽量素材を優先することがよくあります。
- コストの制約: コストは材料の選択において重要な要素です。 高性能材料は高価になる可能性があるため、メーカーは性能と費用対効果のバランスを取る必要があります。
- 企業コンプライアンス: ヘルスケアなどの業界では、材料は生体適合性と安全性に関する厳しい規制基準を満たさなければなりません。
- 商品在庫: 材料とその供給源の入手可能性も選択に影響します。 一部の特殊な合金または複合材料は入手が制限されている場合があります。
B. 材料特性
精密加工には材料の特性を理解することが重要です。 以下にいくつかの主要な材料特性とその重要性を示します。- 抗張力: 引張強さは、破損することなく引張力に耐える材料の能力を測定します。 機械的ストレスを受ける構造コンポーネントや部品には不可欠です。
- 硬度: 硬度は、材料の変形や摩耗に対する耐性を示します。 硬い材料は切削工具に適していますが、シールなどの特定の用途には柔らかい材料が好まれる場合があります。
- 延性: 延性とは、引張応力を受けたときに破損することなく変形する材料の能力を指します。 延性のある材料は成形が容易ですが、剛性が必要な用途には適さない場合があります。
- 熱伝導率:熱伝導率の高い素材が効率よく熱を放散します。 この特性は、温度制御が重要な用途では非常に重要です。
- 電気伝導性: 電気伝導性は、材料が電気の流れを促進する必要があるエレクトロニクスや電気部品において不可欠です。
- 磁気的性質: 磁気特性は、材料が強磁性または非磁性である必要がある電磁気学やエレクトロニクスなどの業界で重要です。
- 耐薬品性: 材料は、酸、塩基、またはその他の腐食性物質にさらされる環境での化学腐食に耐性がなければなりません。
C. 被削性係数
機械加工性とは、材料の機械加工、切断、または成形の容易さを指します。 これは、次のようなさまざまな要因によって影響されます。- 素材硬度: 一般に、柔らかい材料は機械加工が容易ですが、硬い材料には特殊な工具や技術が必要になる場合があります。
- 切りくずの形成: 加工中の切りくずの形成と排出は、プロセスの効率と表面仕上げに影響を与えます。
- 工具の摩耗: 材質が異なると、工具の摩耗の程度が異なり、加工速度とコストに影響を与える可能性があります。
- クーラントと潤滑剤: 加工中の摩擦、熱、工具の摩耗を軽減するには、適切な冷却剤と潤滑剤が不可欠です。
- 切削速度: 切削工具が材料内を移動する速度は、生産性と加工面の品質の両方に影響します。
- 工具材料: 超硬やハイスなどの切削工具材質の選択は、加工する材質によって異なります。
- 切削パラメータ: 送り速度や切込み深さなどの切削パラメータを調整することで、特定の材料の加工プロセスを最適化できます。
精密加工用工作機械
工作機械は精密機械加工の中心であり、原材料を高精度の部品に変えることができます。 このセクションでは、精密加工に使用される XNUMX つの主要なタイプの工作機械、CNC マシニング センター、旋盤、研削盤、EDM (放電加工) について説明します。 これらの機械はそれぞれ、精密部品の製造において独自の役割を果たします。A. CNC マシニング センター
CNC (コンピューター数値制御) マシニング センターは汎用性が高く、精密加工に広く使用されています。 これらは、切削工具とワークピースの動きを非常に正確に制御する自動システムです。 CNC マシニング センターとその重要性の概要は次のとおりです。- 多才: CNC マシニング センターは、フライス加工、穴あけ、タッピングなどのさまざまな機械加工を実行できます。 この多用途性により、複数の機能を備えた複雑な部品の製造が可能になります。
- 高精度: CNC マシンのコンピュータ制御により、正確な工具の位置決めと一貫した結果が保証され、公差が厳しい部品に最適です。
- オートメーション: CNC マシニング センターは、人間の介入を最小限に抑えながら継続的に稼働できます。 この自動化により効率が向上し、エラーのリスクが軽減されます。
- 複雑な形状: 複雑な形状や輪郭の加工に優れているため、複雑なコンポーネントが一般的である航空宇宙などの業界に適しています。
- 再現可能な結果: CNC マシンは優れた再現性を提供し、製造された各部品が設計の仕様と正確に一致することを保証します。
- セットアップ時間の短縮: CNC マシニング センターは、さまざまなタスクを迅速に切り替えるようにプログラムでき、セットアップ時間を最小限に抑え、生産効率を向上させます。
B. 旋盤
旋盤は、切削工具がその外面から材料を除去しながら、工作物を回転させることによって円筒部品を作成するために使用されます。 生産には欠かせないものです シャフト、ピン、および回転対称のその他のコンポーネント。 旋盤に関する重要なポイントは次のとおりです。- 円筒パーツ: 旋盤は、ねじ山や複雑な溝のある部品など、円筒形または管状の部品の製造に特化しています。
- 高速:高速で動作するため、滑らかで正確な仕上げが要求される部品に適しています。
- 単軸動作: ほとんどの旋盤は単軸であり、ワークピースの外面の形状を整えることに重点を置いています。
- 大量生産に効率的: 旋削加工は、材料の無駄を最小限に抑えて部品を量産するのに非常に効率的です。
- 旋盤: 手動および CNC 制御の旋盤は、さまざまな機能を提供する一般的に使用される旋盤です。
C. 研削盤
研削盤は、硬質または研磨性の材料の精密な表面仕上げおよび成形用に設計されています。 これらは、極めて厳しい公差と優れた表面仕上げを実現するために非常に重要です。 研削盤が重要な理由は次のとおりです。- ミクロンレベルの精度: 研削盤はミクロンレベルの精度を達成できるため、最高レベルの精度が要求される用途には不可欠です。
- 材料の除去: 摩耗によって材料を除去し、表面の欠陥を修正し、並外れた平滑性を実現します。
- 工具とカッターの研削: 平面研削に加えて、切削工具を研ぎ、正確なプロファイルを作成するための専用の研削盤があります。
- 多彩な研削方法:平面研削盤、円筒研削盤、センタレス研削盤などの各種研削盤により、さまざまな加工ニーズに対応します。
- 硬化材料: 研削は、従来の機械加工方法が効果的でない可能性がある工具鋼やセラミックなどの硬化材料に特に適しています。
D. EDM(放電加工)
EDM (放電加工) は、放電を使用して材料を成形する、従来とは異なる加工プロセスです。 従来の切削工具では損傷を引き起こす可能性がある、複雑で繊細な部品の作成に最適です。 EDM の主な側面は次のとおりです。- 物理的接触禁止: EDM では工具とワークピースが直接物理的に接触しないため、工具の磨耗や壊れやすい材料への損傷のリスクが最小限に抑えられます。
- 高精度:非常に硬い材質でも高い精度と仕上げ面品質を実現します。
- ワイヤー放電加工機と彫り放電加工機: EDM マシンには主に XNUMX つのタイプがあります。 ワイヤーカット ワイヤー電極を使用する放電加工と、形状を整えた電極を使用する彫り込み放電加工です。
- 複雑な形状: EDM は、複雑なディテールや微細な特徴を備えた、金型やモールドなどの複雑な形状を製造できます。
- 熱影響部: EDM はワークピースで熱を発生しないため、航空宇宙合金などの熱に弱い材料に適しています。
- 遅いプロセス: EDM は他の加工方法と比較して比較的遅いため、少量で高精度の作業に最適です。
切削工具とツーリング
切削工具は精密機械加工の最前線にあり、原材料を高精度の部品に成形、変換する機器です。 このセクションでは、さまざまな種類の切削工具、工具コーティングの重要性、工具の寿命と摩耗に影響を与える要因について説明します。A. 切削工具の種類
精密機械加工は、特定の作業や材料に合わせて設計されたさまざまな切削工具に依存しています。 切削工具の選択は、加工プロセスの効率と精度に大きく影響します。 一般的な切削工具の種類をいくつか示します。- エンドミル: エンドミルはフライス加工に使用される多用途工具です。 複数の切れ刃を備えており、フェーシング、輪郭加工、溝入れなどのさまざまな方法でワークピースから材料を除去できます。
- ドリル: ドリルはワークに穴を開けるために設計されています。 ツイストドリル、センタードリル、刃先交換式ドリルなど、さまざまな形状があります。
- 旋削用インサート: これらは、円筒部品を成形する旋盤で使用されます。 旋削チップは、さまざまな用途に合わせてさまざまな形状と材質で入手できます。
- フライスカッター: フライスには、フェースミル、ボールミル、スロッティングカッターなどのさまざまな形状があり、フライス盤でワークピースにさまざまな形状を作成するために使用されます。
- リーマ: リーマーは、事前に開けられた穴を正確な寸法に仕上げてサイズ調整するために使用されます。 滑らかで正確な穴表面を保証します。
- タップとダイ: ねじ切り加工に使用する切削工具です。 タップは雌ねじを作成し、ダイスは雄ねじを作成します。
- 砥石: 砥石は精密な平面研削に使用される研磨工具です。 さまざまな研磨材と粒度で入手できます。
- ブローチ: ブローチは、キー溝やスプラインなどの内部および外部の形状やプロファイルを切断するために使用される特殊な工具です。
- 座ぐりと皿穴: これらのツールは、穴の周囲に凹みや面取りを作成するために使用されます。 ファスナーs.
- ボーリングバー: ボーリングバーは、既存の穴を正確に拡大するためのボーリング作業に使用されます。
B. 工具コーティング
工具コーティングは、切削工具の性能と耐久性を向上させるために切削工具に塗布される材料の薄い層です。 これらのコーティングにはいくつかの利点があります。- 摩擦の低減: 窒化チタン (TiN) や炭窒化チタン (TiCN) などのコーティングが工具とワークピース間の摩擦を軽減し、よりスムーズな切削と工具寿命の延長につながります。
- 強化された硬度: コーティングは工具の表面の硬度を高め、耐摩耗性を高め、工具の寿命を延ばします。
- 耐熱性の向上: コーティングは加工中に発生する高温に耐えることができるため、熱に関連した工具の摩耗が軽減され、切削速度が向上します。
- 抗ビルドアップ特性: 一部のコーティングには付着防止特性があり、工具の刃先に物質が蓄積するのを防ぎます。
- 潤滑性の向上: コーティングされた工具は潤滑性が向上し、過剰なクーラントの必要性が減り、切りくず排出が促進されます。
C. 工具寿命と摩耗
工具の寿命と摩耗を理解することは、加工プロセスを最適化し、生産コストを最小限に抑えるために非常に重要です。 工具寿命とは、切削工具の交換や再調整が必要になるまでの有効期間を指します。 工具の寿命と摩耗に影響を与える要因はいくつかあります。- 切削速度: 切削速度が高くなると、加工中に発生する温度が高くなるため、工具の摩耗が増加する可能性があります。 工具寿命と生産性のバランスをとるには、切削速度を適切に選択することが不可欠です。
- 送り速度: 切削工具がワークに進入する速度は工具の摩耗に影響します。 送り速度が高いと摩耗が加速する可能性がありますが、送り速度が低いと工具寿命が延びる可能性があります。
- 切り込みの深さ: 切込みの深さは、パスごとに除去される材料の量に影響します。 切り込みが深くなると工具の摩耗が増加する可能性があるため、深さを最適化することが重要です。
- 素材硬度: 硬い材料を切断すると、工具の摩耗が早まる可能性があります。 硬い材料を効果的に加工するには、特殊な工具とコーティングが使用されます。
- クーラントと潤滑剤: 適切な冷却剤と潤滑剤は熱を放散し、摩擦を軽減し、工具の寿命を延ばします。
- 工具材料: 切削工具の材質は耐摩耗性に影響します。 超硬やセラミックなどの材料は優れた耐摩耗性を備えています。
- ツールジオメトリ: すくい角、逃げ角、チップブレーカの設計などの切削工具の形状は、摩耗パターンに重要な役割を果たします。
- 被削材: 加工される材料の種類は工具の摩耗に影響します。 研磨材は工具の摩耗を早める可能性があります。
精密機械加工工程
精密機械加工プロセスは、原材料を厳しい公差と優れた表面仕上げを備えた高精度部品に加工する方法です。 このセクションでは、旋削、フライス加工、穴あけ、研削、放電加工 (EDM) という XNUMX つの主要な精密加工プロセスについて説明します。 これらの各プロセスは独自の目的を果たし、ワークピースの特定の要件に基づいて使用されます。A. 旋削
旋削は、主に円筒部品の成形に使用される機械加工プロセスです。 これには、一点切削工具が外面から材料を除去しながら、ワークピースを回転させることが含まれます。 旋削の重要な側面は次のとおりです。- 円筒パーツ: 旋削加工はシャフト、ピン、スリーブなどの円筒部品の製造に最適です。
- 回転対称性:旋盤でワークを回転させながら切削工具で加工するため、回転対称性が要求される部品に最適です。
- 各種操作:旋削加工により、正面削り、旋削(縮径)、テーパ旋削、ねじ切りなどの多彩な加工が可能です。
- 一点切断: 単一の切削工具が連続動作で材料を除去するため、効率的に材料を除去できます。
- 旋盤: 旋削加工には、手動旋盤と CNC 制御旋盤の両方が一般的に使用されます。
B. フライス加工
フライス加工は、多点切削工具を使用してワークピースから材料を除去する多用途の精密機械加工プロセスです。 幅広い形状や機能の作成に適しています。 フライス加工の主な側面は次のとおりです。- 多才: フライス加工により、平らな表面、スロット、ポケット、および複雑な輪郭を作成できます。 2D 加工と 3D 加工の両方に使用されます。
- 多点切断: ツールの複数の刃先が同時にワークピースと相互作用し、効率的な材料の除去が可能になります。
- フライス加工の種類:エンドミル、フェイスミル、ボールミルなど各種カッターによるフライス加工が可能です。
- CNCマシニングセンター: CNC 制御のフライス盤は工具の動きを正確に制御でき、現代の機械加工で広く使用されています。
- 高速:高速での加工が可能となり、効率的な生産が可能となります。
C. 穴あけ
穴あけ加工は、ワークピースに穴を開けるために使用される精密機械加工プロセスです。 さまざまな業界の基本的な業務です。 掘削の主な側面は次のとおりです。- 穴の作成: ボール盤は、ドリルと呼ばれる特殊なツールを使用して材料を除去し、特定の直径の穴を作成します。
- ドリルの種類: ツイストドリル、センタードリル、刃先交換式ドリルなど、それぞれ特定の用途に合わせて設計されたさまざまなタイプのドリルが用意されています。
- 正確さ: 穴を正確に作成するには、穴あけ加工において正確な位置決めと位置合わせが不可欠です。
- 速度と送り速度: 回転速度や送り速度などの穴あけパラメータは、希望の穴寸法を実現するために重要です。
- クーラントと潤滑剤: 適切な冷却剤と潤滑剤を使用して、穴あけ中の熱を放散し、摩擦を軽減します。
D. 研削
研削は、砥石車を使用して材料を除去し、非常に厳しい公差と表面仕上げを実現する精密機械加工プロセスです。 研削の主な側面は次のとおりです。- 並外れた精度: 研削はミクロンレベルの精度を達成できるため、最高の精度が必要な用途に最適です。
- 表面仕上げ: 優れた表面仕上げが得られるため、多くの場合、追加の仕上げプロセスが不要になります。
- 材料: 研削は、焼入鋼、セラミック、超硬などの硬質で研磨性の高い材料に適しています。
- 多彩な研削方法:平面研削盤、円筒研削盤、センタレス研削盤などの各種研削盤により、さまざまな加工ニーズに対応します。
- クーラント: 過熱を防ぎ、ホイールの完全性を維持するために、適切なクーラントは研削において不可欠です。
E. 放電加工 (EDM)
EDM (放電加工) は、放電を使用して材料を除去する、従来とは異なる精密加工プロセスです。 特に複雑に入り組んだ形状や硬質・耐熱性の材料の加工に適しています。 EDM の主な側面は次のとおりです。- 非接触加工: EDM では工具とワークピースが直接接触しないため、工具の摩耗や損傷のリスクが軽減されます。
- 高精度: EDM は高精度を達成できるため、厳しい公差が不可欠な用途に適しています。
- 複雑な形状:複雑な形状、金型、金型、細部の部品の加工に優れています。
- ワイヤー放電加工機と彫り放電加工機: 放電加工機には主に XNUMX つのタイプがあります。ワイヤー電極を使用するワイヤー放電加工と、成形された電極を使用する彫り込み放電加工です。
- 遅いプロセス: EDM は他の加工方法と比較して比較的遅いため、少量で高精度の作業に最適です。
公差と品質管理
精密機械加工では、部品が指定された基準を確実に満たすように、細部への細心の注意と品質管理への厳格な取り組みが必要です。 このセクションでは、精密機械加工における品質管理の XNUMX つの重要な側面、すなわち幾何寸法および公差 (GD&T)、統計的工程管理 (SPC)、および品質保証について説明します。A. 幾何寸法および公差 (GD&T)
GD&T と略されることもある幾何学寸法および公差は、部品上のフィーチャーのサイズ、形状、向き、および位置の許容変動を定義し、伝達するために使用されるシステムです。 GD&T は次の理由から精密加工に不可欠です。- 正確なコミュニケーション: GD&T は、エンジニア、設計者、機械工が設計意図と寸法要件を正確に伝えるための標準化された言語を提供します。
- 公差の明確化: これは、重要な寸法の許容可能な変動を定義し、すべての関係者が許容される変動を確実に理解できるようにするのに役立ちます。
- 強化された品質: GD&T は、設計仕様のあいまいさを減らし、加工中のエラーのリスクを最小限に抑えることで品質の向上を促進します。
- コスト効率: 明確な GD&T 仕様は、誤解や誤解によって部品が廃棄されたり、再加工が必要になったりする可能性が低くなるため、製造コストの削減につながります。
- 複雑な形状: 複雑な形状の部品に特に役立ち、すべてのフィーチャーが希望の仕様に合わせて製造されるようになります。
B. 統計的プロセス管理 (SPC)
統計的プロセス制御 (SPC) は、統計的手法を使用して機械加工プロセスを監視および制御する品質管理手法です。 SPC は次の理由から精密加工に不可欠です。- プロセス監視: SPC は、加工プロセスをリアルタイムで監視し、必要なパラメータからの変動や逸脱を特定するのに役立ちます。
- 問題の早期発見: SPC はプロセスを継続的に監視することで、規格外の部品につながる可能性のある問題を早期に検出し、無駄ややり直しを削減します。
- データ主導の意思決定: SPC は、データと統計分析に基づいてプロセス調整に関する情報に基づいた意思決定を行い、機械加工プロセスが許容範囲内に収まるようにします。
- 一貫性の向上: SPC はプロセスの一貫性を促進し、不適合部品が生成される可能性を減らします。
- スクラップと再加工の削減: SPC は、プロセスの変動を迅速に特定して対処することで、不良部品の生産を最小限に抑え、スクラップや再加工のコストを削減します。
C. 精密加工における品質保証
精密機械加工における品質保証には、製造された部品が指定された品質基準を満たしているか、それを超えていることを保証するための包括的なアプローチが含まれます。 これには、次のようなさまざまな要素が含まれます。- プロセスドキュメント: 標準作業手順 (SOP) や作業指示を含む機械加工プロセスの詳細な文書化により、各ステップが一貫して実行されることが保証されます。
- 検査・測定: 精密機器と計測技術を使用した厳格な検査と測定により、部品が指定された公差と品質基準に適合していることが確認されます。
- キャリブレーション: 精度とトレーサビリティを維持するには、加工装置や測定器の定期的な校正が不可欠です。
- 材料検証: 使用される材料が設計要件を満たしていることを確認するには、材料の特性、組成、品質を検証することが重要です。
- 従業員研修: 機械工や品質管理担当者向けのトレーニングとスキル開発プログラムにより、彼らがその役割と責任を確実に遂行できるようになります。
- 根本原因分析: 不適合部品が特定されると、根本原因分析が行われ、問題の原因が特定され、是正措置が実行されます。
- 継続的改善: 継続的な改善の文化はイノベーションを促進し、機械加工プロセスと品質管理手順の継続的な強化を推進します。
- 顧客フィードバック: 顧客からのフィードバックを収集して分析することは、改善すべき領域を特定し、機械加工プロセスを顧客の期待に合わせるのに役立ちます。